
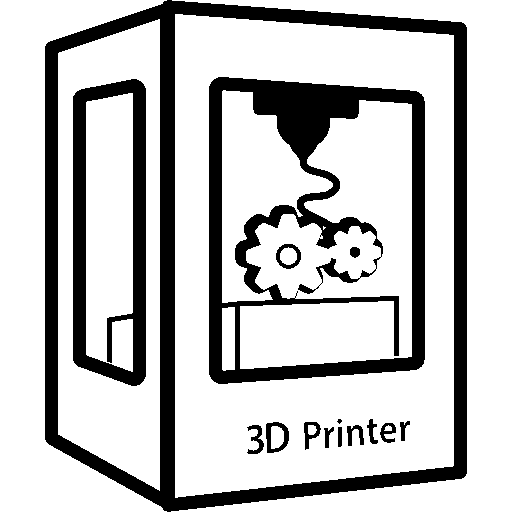
Thanks so much. I did not know the original purpose of the profile. In my experience with 3d printing, the buttress profile strength is in the opposite orientation when printed vertically. The additional length of the tapered profile creates a better distributed load across more layers of the stretching member/fastener. Still, I will prioritize overall printability without supports over thread directional orientation in most cases. I’m usually using a very large custom sized thread where the thread strength is irrelevant.
Like here in my laptop GPU water cooler project, I am using a buttress thread and spline to retain the cooling block and pump.
Walls are too thin for a bottle and with the cut for r&i I would expect it to have issues at the seam. Even with this, the seam requires holding until it starts to get touching contact. Maybe if the bottle is extended past the 45°-50° tangent it would do a little better but then it has drop potential, especially with this PC/ABS blend and no part fan in an enclosure.